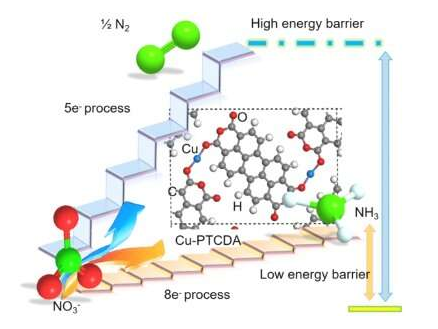
Ammonia (NH3) is a colorless, gaseous and water-soluble compound used in several sectors, including agriculture, the energy sector, and a variety of industries. For over a century, the main way of producing large quantities of ammonia has been via the Haber-Bosch process, which entails the use of high pressure to produce a chemical reaction that enables the direct synthesis of ammonia from hydrogen and nitrogen.
While the Haber-Bosch process enables the mass production of ammonia, it is known to be harmful for both humans and the environment, as it involves the consumption of fossil fuels and thus aggravates the greenhouse effect. Due to these undesirable effects, researchers have sought alternative methods for producing ammonia via N2?H2Ochemical reactionsunder ambient conditions, some of which utilize renewable energy sources.
Some of these new techniques for the production of ammonia have been found to be effective and relatively inexpensive. Nonetheless, they typically only allowed researchers to produce limited quantities of ammonia and exhibited a poor selectivity, due to the inert N≡N bond and the ultralow solubility of N2in water.
Researchers at South China University of Technology and Argonne National Laboratory have recently devised a new electrochemical strategy to produce ammonia through the reduction of nitrate. Their method, introduced ina paper published inNature Energy, is based on the use of a copper-molecular solid catalyst.
"Obtaining NH3directly from non?N2sources is considered a revolutionary strategy to address the concerns associated with previous ammonia production processes," Haihui Wang, one of the researchers who carried out the study, told Phys.org. "In the search fornitrogen-containing alternatives other than N2to synthesize NH3, the nitrate anion (NO3-) stands out due to the fact that the lower dissociation energy of N=O bond (204 kJ mol-1) compared with N-N triple bond (941 kJ mol-1), and the enrichment of NO3-in water resources caused environmental pollution and threatens human health."
Selectively converting NO3-to NH3under ambient conditions and in a H2O-based system could be a greener alternative for the mass production of NH3. This alternative conversion would alleviate the environmental problems associated with current methods for producing ammonia on a large scale, while also decreasing energy consumption.
"Converting NO3?into NH3is far from an easy task, as it requires an eight-electron transfer reaction as well as a slightly lower reaction potential (i.e., 1.20 V versus the reversible hydrogen electrode or RHE) than that of the five?electron conversion of NO3?to N2(1.25 V versus RHE)," Wang explained. "Various electrocatalytic systems with different heterogeneous catalysts (such as Cu, Ag, Au, and so on) have been proposed in the past, but most of them tend to produce N2via five-electron reduction of NO3-rather than the desired eight-electron reduction."
The practical potential of converting NO3-to NH3is below what is known as the hydrogen evolution reaction (HER) potential, which leads to the generation of H2. This can reduce the overall efficiency of the production of NH3.
In their study, Wang and his colleagues were able to achieve the direct eight-electron reduction of NO3-to NH3,catalyzed by Cu-incorporated crystalline 3,4,9,10-perylenetetracarboxylic dianhydride (PTCDA) with a low energy barrier way. The catalyst they used exhibited a high yield rate and outstanding selectivity, effectively suppressing HER.
"We screened catalysts with the preparation of a series of metals incorporated in PTCDA, such as Cu, Ag, Au, Ru, Rh, Ir, Pd, Pt, Bi, Ti, Cr, Mn, Fe, Co, Ni, Y, Zr, Mo, La and Ce," Wang explained. "We found that the high performance of our catalyst can be attributed to the unique electron configuration of Cu 3dorbital showing increased overlap with nitrate O 2porbitals to enhance charge transfer, as well as the structure of PTCDA, which helps to regulate the transfer of protons and electrons to the active Cu centers and then to inhibit HER and promote H-N binding."
The electrochemical method introduced by Wang and his colleagues could address the challenges currently associated with mass NH3production. In initial tests, this method achieved Faradaic efficiencies between 60% and 86% and NH3production rates between approximately 400 and 900 μg h–1cm–2at applied potentials of ?0.4 to ?0.6 V versus RHE.
The results are significantly better than those achieved using other methods for the electrochemical reduction of N2to NH3. For example, lithium-mediated methods, which are the most known for achieving relatively high yield rates in the electroreduction of N2-to-NH3, achieved a production rate of less than 36 μg h-1cm.
The recent study by Wang and his colleagues also opens up new possibilities for the recycling of nitrogen (NO3-) in wastewater. For several years, NO3-was considered to be a toxic water contaminant and was usually transferred into gaseous nitrogen and returned to the air. Recent studies, however, suggest that the high amount of nitrogen in wastewater could in fact be recycled for fertilization.
"The total nitrogendischarged into the water per year is 14.5 ± 3.1 million tons in China, which is about 50% of the annual consumption of synthetic nitrogen (300.5 million tons in 2016)," Wang said. "In 2016, the United States planted 94 million acres of corn, using about 8.9 billion kilograms of nitrogen annually, which accounts for 40% of the annual nitrogen use in the United States. However, it is worth noting that2.4 billion kilograms of nitrogen is available in wastewater each year.The statistics prove that nitrogen in wastewaters could be a valuable resource."
In addition to allowing the large-scale production of ammonia in ways that are more environmentally friendly, the recent work by Wang and his colleagues could pave the way toward the development of wastewater management systems with nitrogen conversion capabilities. These systems would enable the recycling of large quantities of nitrogen, ultimately optimizing the use of global resources and protecting the environment.
While the results are promising, the researchers still need to overcome two technical challenges before their method can be applied in real-world settings. These challenges will be the main focus of their next set of studies.
"On the one hand, our future studies will be aimed at enhancing the catalyst's structure to further improve its long-term stability," Wang said. "In this work, the NH3yield rate decreased from 337.8 μg h-1cm-2to 140.3 μg h-1cm-2after 15 hours, after which it was substantially stable and maintained an NH3yield rate of 130.8 μg h-1cm-2after 40 hours. On the other hand, we will work on the large-scale application of NH3electrosynthesis, developing an electric-driving flow device for the direct and continuous mass production of high-purity liquidammoniaor ammonium salt. We plan to devise a simple method for the direct purification and collection of the products, which removes the need for additional purification, transportation and other procedures."
Explore further
Achieving highly efficient ammonia synthesis by altering the rate-determining step
More information:Electrochemical reduction of nitrate to ammonia via direct eight-electron transfer using a copper-molecular solid catalyst.Nature Energy(2020).DOI: 10.1038/s41560-020-0654-1.
Managing nitrogen to restore water quality in China.Nature(2020).DOI: 10.1038/s41586-019-1001-1
Recycling fertilizer.Nature(2020).DOI: 10.1038/s41560-020-0670-1
Journal information:Nature Energy,Nature